Time-Of-Flight Diffraction (TOFD)
Time-Of-Flight Diffraction (TOFD) is a technique based on time of flight of waves and the diffraction produced by the extremities of the discontinuity. TOFD consists of a pair of transducers facing each other on angled wedges de-fined to produce longitudinal waves. One pulses while the other receives, and are separated by a known distance that ensures coverage of the desired zone.
TOFD is recognized for its high level of accuracy and precision regarding sizing. It is complemented by PAUT or Conven-tional UT in order to cover the top and bottom dead zones.

These technologies has ability to collect and encode full volumetric data, PAUT and ToFD brings code compli-ance and auditable results to the everyday ultrasonic examination. This makes Phased Array and ToFD an effective and efficient alternative to Radiographic inspection. Since there is no radiation or environmental hazards, Phased Array and ToFD inspections can access radiation sensitive areas, increase project production by not displacing other working teams in the area, and maximizes on-site and personnel safety.
Advantages of TOFD
- Excellent repeatability, high level of sensitivity & better flaw characterization and sizing.
- Increased coverage of the area of interest than with a single probe and wedge.
- Increased Probability of Detection (PoD) during weld inspection.
- Increased speed of inspection.
- Data recording for future analysis/record-keeping.
- Ability to inspect complex geometries
- Detection of both embedded flaws and surface connected ones
Applications
Focus Integrity solutions PAUT and ToFD inspection services are an accurate, efficient, and reliable volumetric ex-amination technique offering real-time imaging to reliably detect discontinuities in all the below mentioned applica-tions. Our PAUT & ToFD inspection specialists are cross trained two perform work in Power Generation, Oil & Gas, Chemical and other industries.
Damage specific Solutions
• Stress Corrosion Cracking (SCC) inspection.
• Stress – oriented hydrogen induced cracking (SOHIC).
• High Temperature Hydrogen Attack (HTHA) inspection.
• Detection of creep damage in reformer tubes.
• Detection of carburization in furnace tubes.
• Accurate flaw Sizing data for Fitness – For – Service (FFS) calculations.
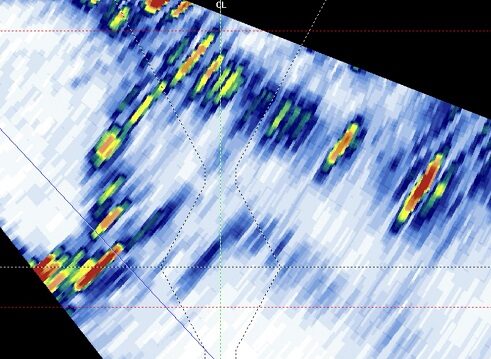
General Applications
• Weld Inspection for flaw detection and sizing.
• (Carbon Steel, Alloy Steel, Stainless Steel and Inconel Alloys)
• Pressure vessle.
• Pipeline and piping.
• Low diameter and low thickness boiler tubes
• High thickness claded and non claded reactors.
• orrosion Mapping
• Corrosion Mapping on bends using flexible PAUT probes.
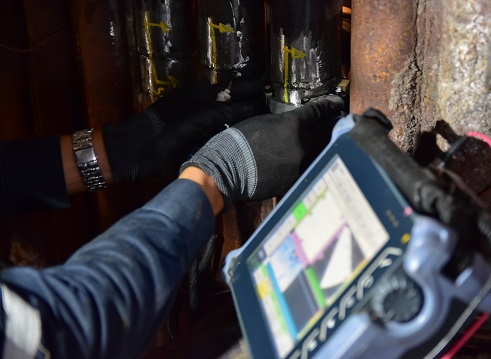
Special Applications
• Turbine blades and christmas tree designs.
• Skirt weld joint of coke drum.
• Aerospace and wind turbine blades fabricated with composite materials.
• Internal Rotary Inspection System (IRIS) for heat ex-changer tubes.
• Rotary inspection system for tube to tube sheet joints.
• Railwheel and track testing.
• Any other complex geometry where ultrasonic testing is possible.
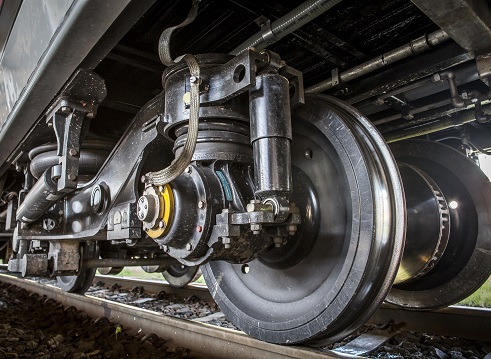